La evaluación de riesgos es fundamental para la protección de las máquinas. El objetivo de un sistema de seguridad es reducir el riesgo a un nivel aceptable, definiéndose el riesgo como un par de tarea y peligro. Si la evaluación de riesgos y la reducción de riesgos se implementan correctamente, el sistema de seguridad será parte integral de la máquina y permitirá a los empleados un acceso seguro para realizar las tareas requeridas de forma segura pero sin obstáculos. Es probable que se pase por alto o se eluda un sistema de seguridad oneroso por motivos de conveniencia y productividad. La medida de reducción de riesgos no debería crear nuevos peligros.
El proceso de evaluación de riesgos incluye los pasos de analizar los riesgos inherentes de la máquina, las tareas que hacen que las personas estén expuestas a esos riesgos inherentes y, en última instancia, incluye la aplicación de métodos de reducción de riesgos, así como la documentación de los resultados. Todo el proceso también debe considerarse como un proceso iterativo en el que se evalúan todos los pares de tareas y peligros en cuanto a gravedad, frecuencia y posibilidad de evitarlos. El resultado de la evaluación de riesgos sería una recomendación de categoría y/o nivel de desempeño que las medidas de reducción de riesgos deben cumplir.
Si el riesgo residual no se considera aceptable (tolerable), entonces se debe repetir el proceso para determinar qué medidas de reducción adicionales deben aplicarse. Sin embargo, la evaluación de riesgos también permite que no todos los riesgos puedan eliminarse o reducirse dentro de límites económicos razonables. Si se determina que el riesgo residual es aceptable o no es, en última instancia, responsabilidad del usuario final.
El mejor enfoque para realizar una evaluación de riesgos es en equipo, incluyendo personas externas, permitiendo la aportación de diferentes opiniones sobre qué tareas deben realizarse y qué peligros existen. ANSI B11.0: 2020 ahora incluye una lista de responsabilidades para el proveedor y usuario de maquinaria y recomienda puntos de posible colaboración. La evaluación debería ampliarse más allá de los daños humanos para cubrir los daños a la máquina y otros activos de la empresa, así como los daños al medio ambiente. Esto dará como resultado un lugar de trabajo más seguro y eficiente. Esto no significa que el fabricante pueda eliminar todos los riesgos. El fabricante debe identificar y comunicar cualquier riesgo residual al usuario final.
Pasos de Estimación de Riesgos según ISO 12100 y ANSI B11.0
ISO 12100 y ANSI B11.0 brindan orientación para el proceso de evaluación de riesgos que consiste en la estimación y reducción de riesgos. Los diagramas de flujo a continuación describen los procesos de evaluación de riesgos para ISO 12100 y ANSI B11.0. Si bien parecen ligeramente diferentes, los dos procesos son casi idénticos.
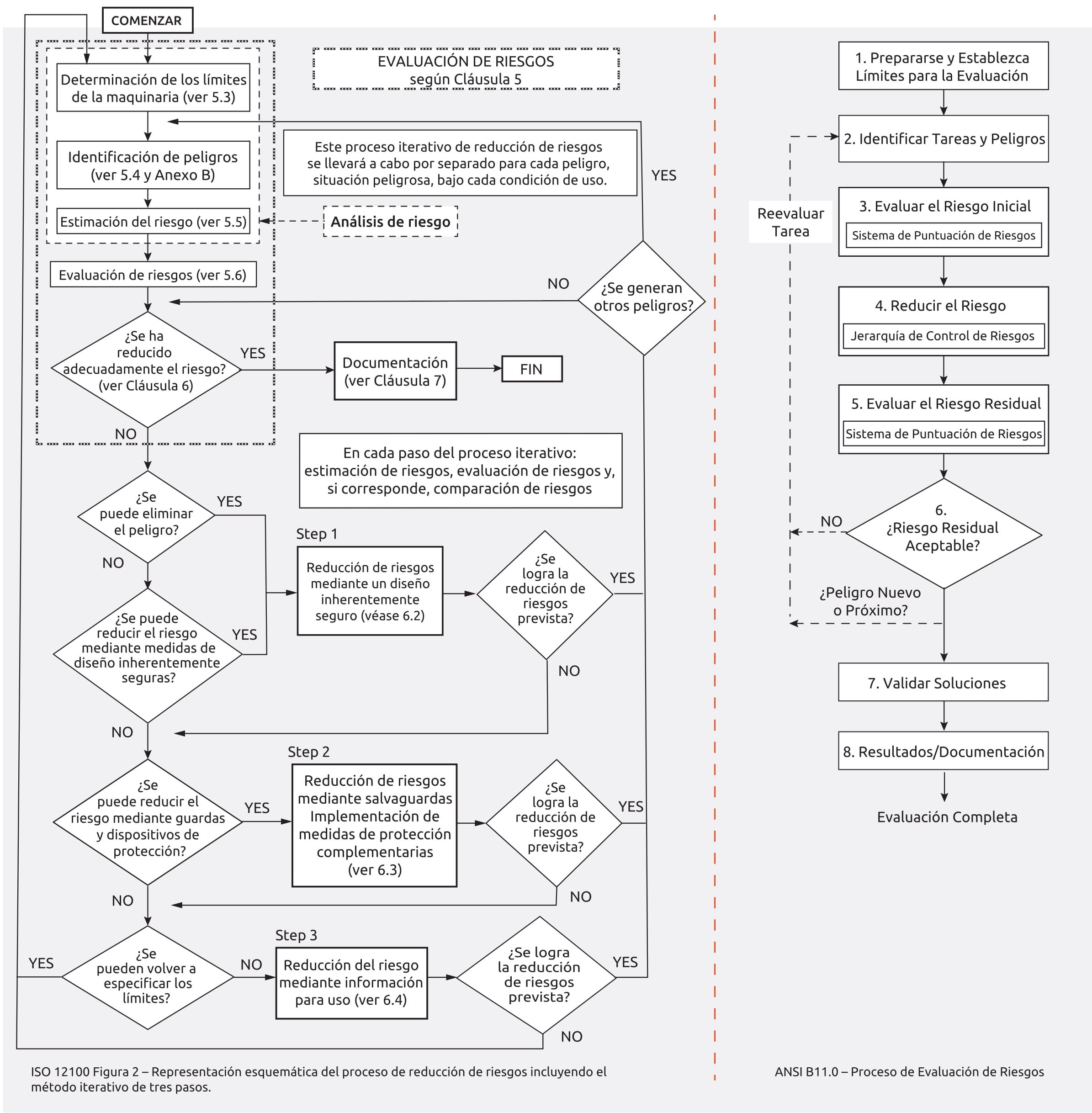
El paso 1 es determinar los límites y el alcance de la maquinaria y la evaluación.
El paso 2 es identificar las tareas y los peligros asociados. Esto incluye a las personas afectadas, las tareas que realizan y los peligros a los que están expuestas. Es importante no pasar por alto los peligros asociados con las partes de potencia fluida del sistema de seguridad.
El paso 3 incluye una estimación inicial del riesgo para determinar qué nivel de reducción del riesgo se requiere. Existen numerosas herramientas de estimación de evaluación de riesgos disponibles. Seleccionar una que sea mejor para usted es un paso crítico.
ANSI B11.0 Estimación de Riesgos
La matriz de estimación de riesgos ANSI B11.0 que se muestra a continuación utiliza Severidad y Probabilidad para calificar los riesgos identificados. Hay cuatro opciones cada una para la gravedad del daño y la probabilidad de que ocurra. Estos se definen en ANSI B11.0 sección 6.4.2.
Probabilidad de ocurrencia del daño | Gravedad del daño | |||
---|---|---|---|---|
Catastrófico | Grave | Moderado | Menor | |
Muy probable | Alto | Alto | Alto | Medio |
Probable | Alto | Alto | Medio | Bajo |
Improbable | Medio | Medio | Bajo | Despreciable |
Remoto | Bajo | Bajo | Despreciable | Despreciable |
Estimación de Riesgos ISO 13849-1
ISO 13849-1 tiene su propio método para determinar el nivel de desempeño requerido. Tiene tres factores en lugar de dos: gravedad de la lesión, frecuencia de exposición y posibilidad de evitarla; pero sólo proporciona dos opciones para cada factor. La herramienta de estimación de riesgos proporciona un nivel de desempeño (PLr) requerido a, b, c, d o e.
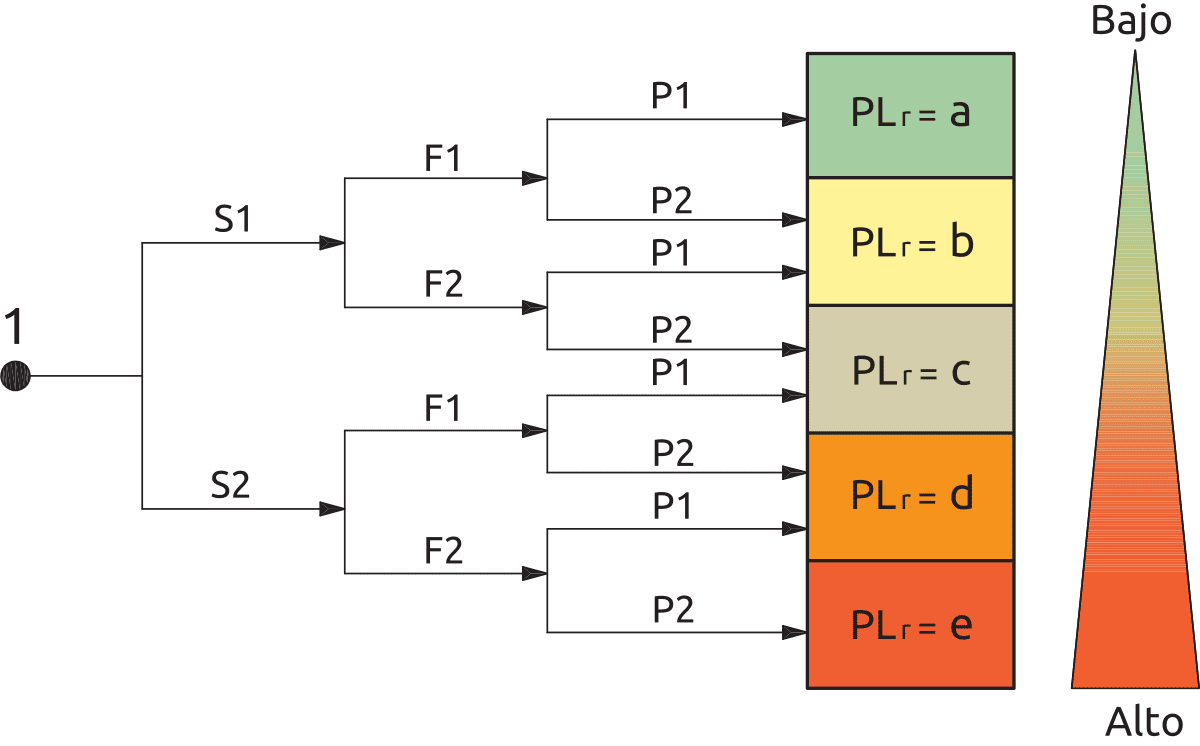
H Alta contribución a la reducción de riesgos
PLr Nivel de desempeño requerido
S1 Leve (lesión normalmente reversible)
S2 Grave (lesión normalmente irreversible o muerte)
F Frecuencia y/o tiempo de exposición al peligro
F1 Ocasional-a-poco frecuente y/o el tiempo de exposición es corto
F2 Frecuente-a-continuo y/o el tiempo de exposición es largo
P Posibilidad de evitar o limitar el daño
P1 Posible bajo condiciones específicas
P2 Apenas posible
Ejemplo de Estimación de Riesgo ANSI/RIA TR15.306
ANSI/RIA TR15.306 utiliza un enfoque híbrido que es similar a los métodos ANSI B11.0 e ISO 13849-1 para determinar el nivel de desempeño y la categoría requerida. Tiene tres factores como la metodología ISO 13849-1, pero resulta en términos similares al enfoque ANSI B11.0.
Se utiliza una tabla adicional para definir los requisitos de desempeño, muy similar a la metodología ANSI B11.0.

Nivel de Riesgo | Requisitos mínimos de SRP/CS | |
---|---|---|
Pl R | Structure Category | |
Despreciable | c | 1 |
Bajo | c | 2 |
Medio | d | 2 |
Alto | d | 3 |
Muy Alto | e | 4 |
Evaluación de Riesgos de Potencia Fluida
Considerar:
- ¿El sistema neumático o hidráulico provoca movimiento?
- ¿El sistema neumático o hidráulico podría provocar pinchazos, cortes o puntos de perforación?
- ¿Desactivar la presión neumática o hidráulica puede hacer que las cosas se muevan?
- ¿Podría la fuerza gravitacional tener algún efecto?
Si hay puntos de pellizco, puntos de corte y puntos de perforación causados por dispositivos de potencia de fluida, se deben abordar estos peligros. Tómese el tiempo para comprender los posibles modos de falla de las válvulas utilizadas en el sistema; y la gravedad asociada con los peligros según las presiones y fuerzas que se utilizan en el sistema neumático o hidráulico.
Cada actuador de potencia de fluida (cilindro o de otro tipo) en el sistema de la máquina debe evaluarse en cuanto a cómo se controla y qué presiones se aplican para determinar las fuerzas que pueden generarse. Luego se debe examinar el esquema de control de las válvulas en el sistema para determinar las condiciones normales y de falla del circuito de potencia del fluida. Por último, es importante considerar qué sucede cuando ocurre un evento de seguridad y, por lo tanto, es crucial determinar qué harán los actuadores cuando las válvulas estén des energizadas o si ocurre una falla.